More Power, More Performance, More Connectivity
Expanding upon the groundbreaking IDEC FC6A Micro PLC, the FC6A Plus can control large machines or entire small-scale manufacturing facilities with:
- Up to 2060 I/O, with a maximum of 511 analog I/O
- Extremely fast basic instruction execution of 21 nanoseconds
- 800 kB (100K steps) of program memory
- Extensive data memory, more than double the capacity of a typical micro PLC
FC6A Series MicroSmart Plus
Superior Design
Dual RJ45 Ethernet Port
USB Bus Power
Replaceable Battery
Cartridge Expansion or HMI Module
SD Memory Slot
Removable Terminal Blocks
Up to 63 Expansion Modules
Bluetooth, Analog & Discrete I/O Cartridges
One port is configured for office network and the second port is configured for control network. Flawless maintenance and control.
The MicroSmart PLC’s USB port can be used to transfer its software program from a PC to the CPU without connecting a power supply. The USB connection from the PC also provides power to the CPU, so it doesn’t have to be plugged in for program upload or download, or for monitoring by a PC.
The MicroSmart PLC’s battery can be easily replaced. Warning of low battery level is provided both at the CPU via an LED, and through a special data register which can be used to trigger an alarm on the HMI or send an email alert.
Battery indicator using special data register D8056. Could trigger alarm on HMI or send Email alert to replace new battery.
- Cartridge Expansion Module Features:
- Ability to expand digital, analog, serial or Bluetooth cartridges
- Up to two cartridges can be configures
- HMI Module Features:
- An optional HMI module can be added to provide operator interface. It’s a great way to provide visual indication and allow the operators to adjust any parameters in the PLC. The HMI module can also accommodate an optional plug-in analog cartridge, and it has an integral Ethernet port.
- Data Logging – critical for applications that require record keeping such as Pharmaceutical and Medical industries
- Store and transfer user program
- OEM can easily update their machines program using standard SD Memory card
- Convenient and cost effective
- Update Firmware for CPU and expansion modules can easily be updated using SD memory card
- Recipe Functions
- Recipe files can be read from and written to the SD memory card
Simplifies wiring, installation and module replacement- just wire a terminal block and plug it into a module.
Up to 63 expansion modules make the MicroSmart FC6A Plus the most powerfule in the market.
These cost-effective I/O cartridges allow users to add I/O point and Bluetooth communication.
Ultimate Performance
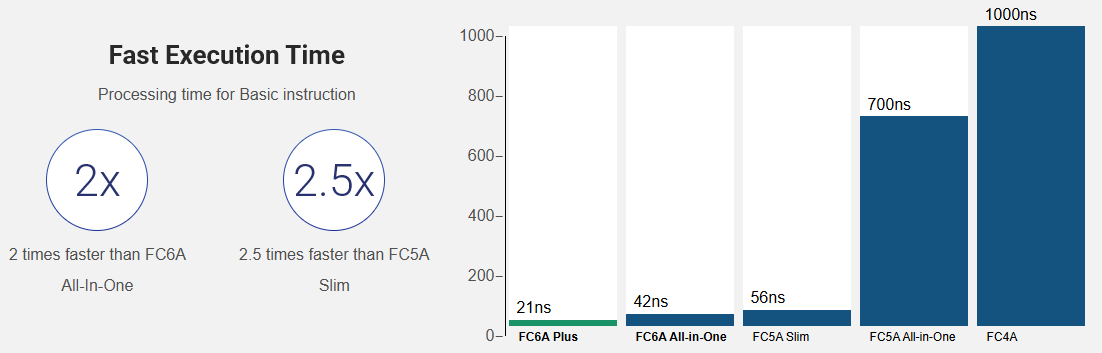
Maximum 2,060 Digital and 511 Analog I/O
Up to 63 digital I/O expansion modules can be configured
FC6A Plus | FC6A All-in-One | FC5A Slim | FC5A All-in-One | FC4A | FT1A | |
---|---|---|---|---|---|---|
Maximum Digital I/O | 2,060 | 520 | 512 | 88 | 512 | 48 |
Maximum Analog I/O | 511 | 126 | 56 | 32 | 56 | 6 |
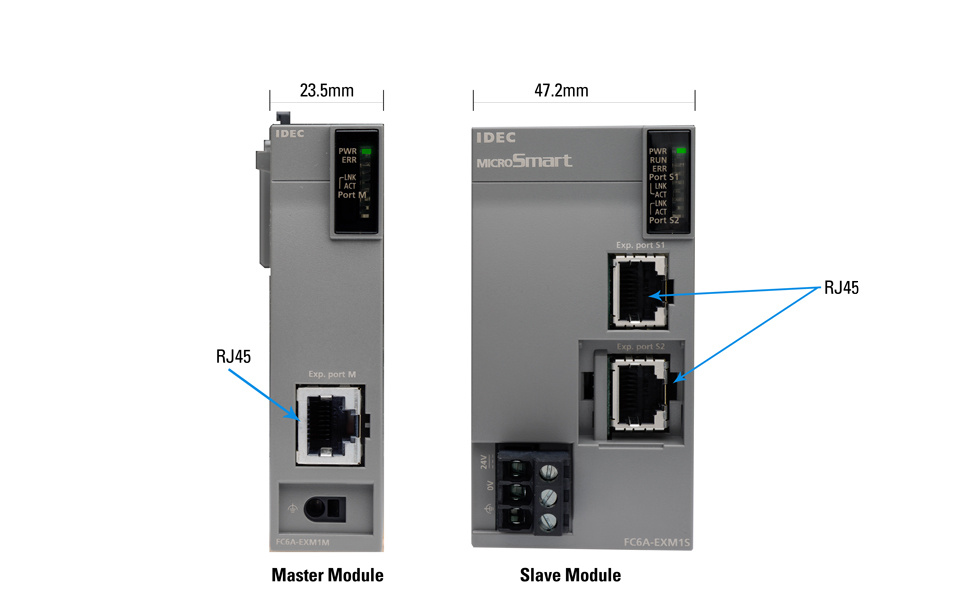
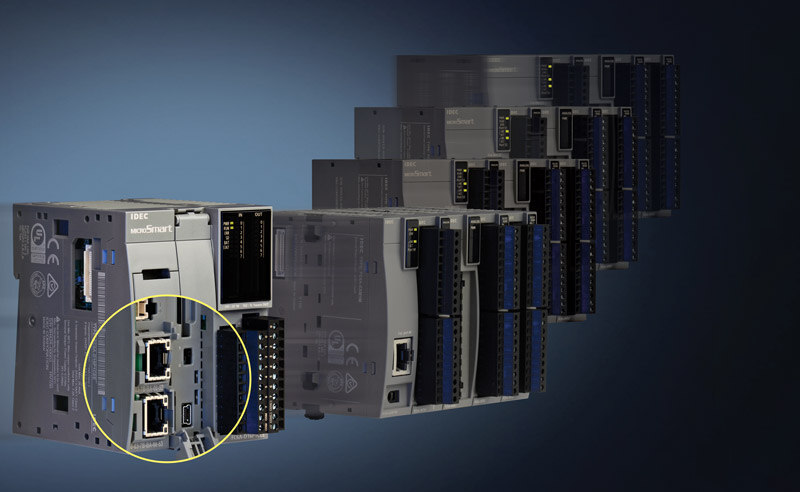
Enormous 800kB (100,000 steps) programming memory
Handle large and more sophisticated program for bigger systems.
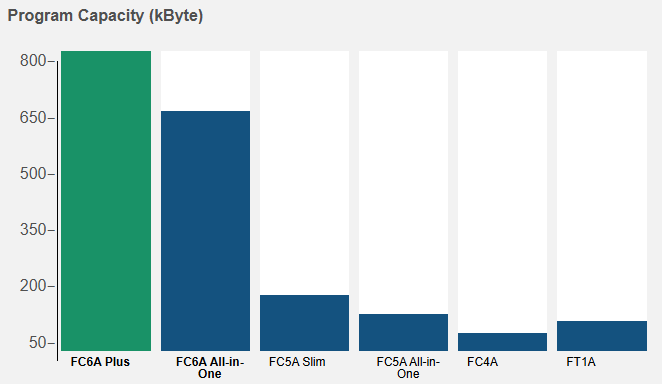
Abundant Data Memory
You get more of everything!
Features | FC6A Plus | FC6A All-in-One | FC5A Slim | FC5A All-in-One | FC4A | FT1A |
![]()
|
![]()
|
![]()
|
![]()
|
![]()
|
![]()
|
|
Program Memory | 800kb | 384 Kb 640Kb (J1939) |
128 Kb | 52 Kb | 31 Kb | 47 Kb |
Data Memory (Data Register) | 260,000 | 56,000 | 48,000 | 2,000 | 7,600 | 2,000 |
Bit Memory (M bit) | 15,400 | 12,400 | 2,048 | 2,048 | 1,584 | 1,024 |
Timer | 2,000 | 1,024 | 256 | 256 | 100 | 200 |
Counter | 512 | 512 | 256 | 256 | 100 | 200 |
Maximum 33 Serial Communication Ports
With the new combo RS232C/RS485 expansion module, up to 15 modules can be configured on the FC6A Plus system. Since both RS232C and RS485 can be used in parallel, a maximum of 30 serial communication ports can be configured. With 2 additional ports can be configured in the Expansion Base Module, a total of 33 serial communication ports can be utilized in the FC6A Plus system.
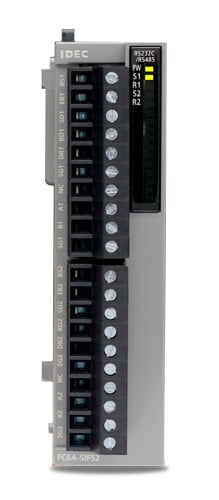
Built-in Real Time Clock
The MicroSmart PLC has a built-in real-time clock. Alternatively, the PLC can obtain time information from an SNTP server for time-based applications such as lighting controls.
Maximum 33 Serial Communication Ports
The CPU and expansion modules have field-upgradeable firmware, making it easy to keep the MicroSmart PLC up to date.- Always get the latest features
- No need to worry about old modules that not compatible with new features
- Your machines can stay ahead of the curve years down the road
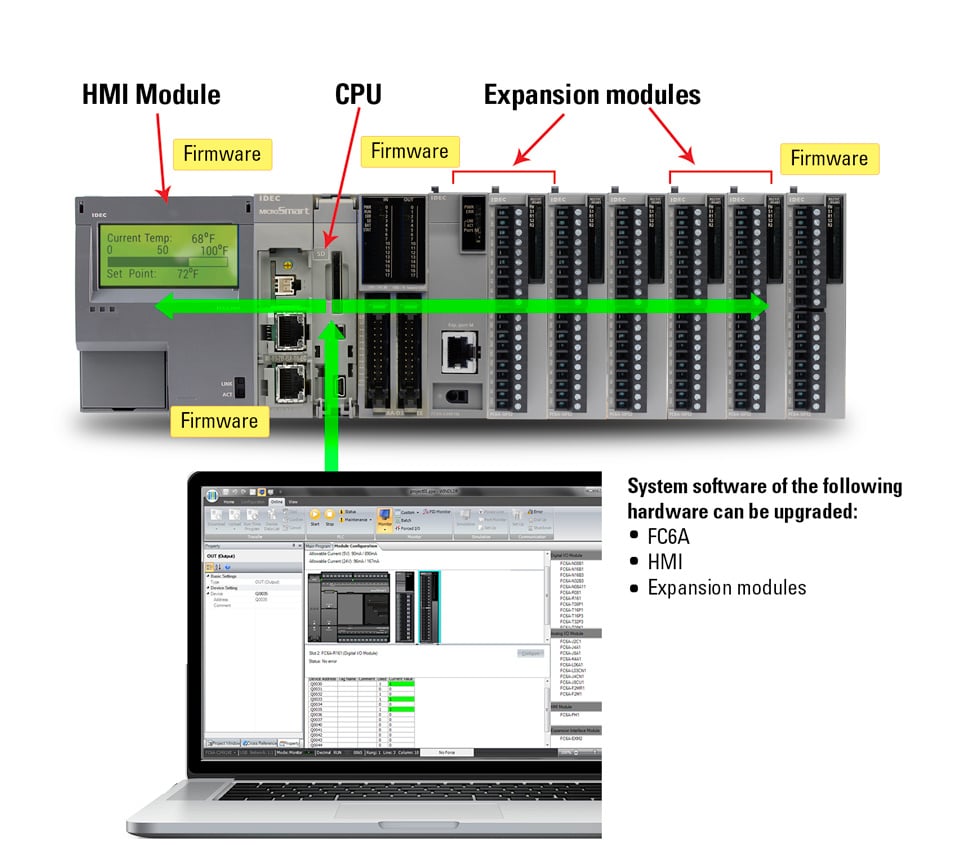
MicroSmart FC6A Plus |
|||||
![]()
|
![]()
|
||||
Sparkplug B EtherNet/IP BACnet/IP Modbus TCP Modbus RTU User Communication (Serial, TCP/UDP) FTP Client/Server Bluetooth (optional cartridge) |
Sparkplug B EtherNet/IP BACnet/IP Modbus TCP Modbus RTU User Communication (Serial, TCP/UDP) FTP Client/Server Bluetooth (optional cartridge) |
||||
Internal Bit: 15,400 Timer: 2,000 Counter: 512 |
Internal Bit: 15,400 Timer: 2,000 Counter: 512 |
||||
Web Server Function Email/Text Notification Web Page Creation Tool |
IIoT Ready
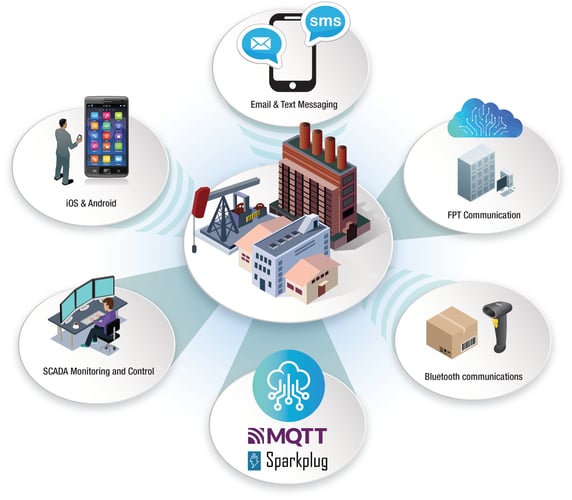
MQTT
MQTT (Message Queuing Telemetry Transport) is a lightweight, publish-subscribe messaging protocol designed for minimal network bandwidth and reliable communication. It is widely used in IoT (Internet of Things) applications where devices need to exchange data efficiently, even over low-bandwidth or unreliable networks.
The IDEC FC6A Plus PLC supports MQTT, enabling direct integration with leading cloud platforms like AWS IoT Core and Microsoft Azure. By connecting to AWS or Azure, the FC6A Plus empowers users to build advanced IoT and IIoT solutions, enabling predictive maintenance, remote system management, and data-driven decision-making for smart factories and connected application.
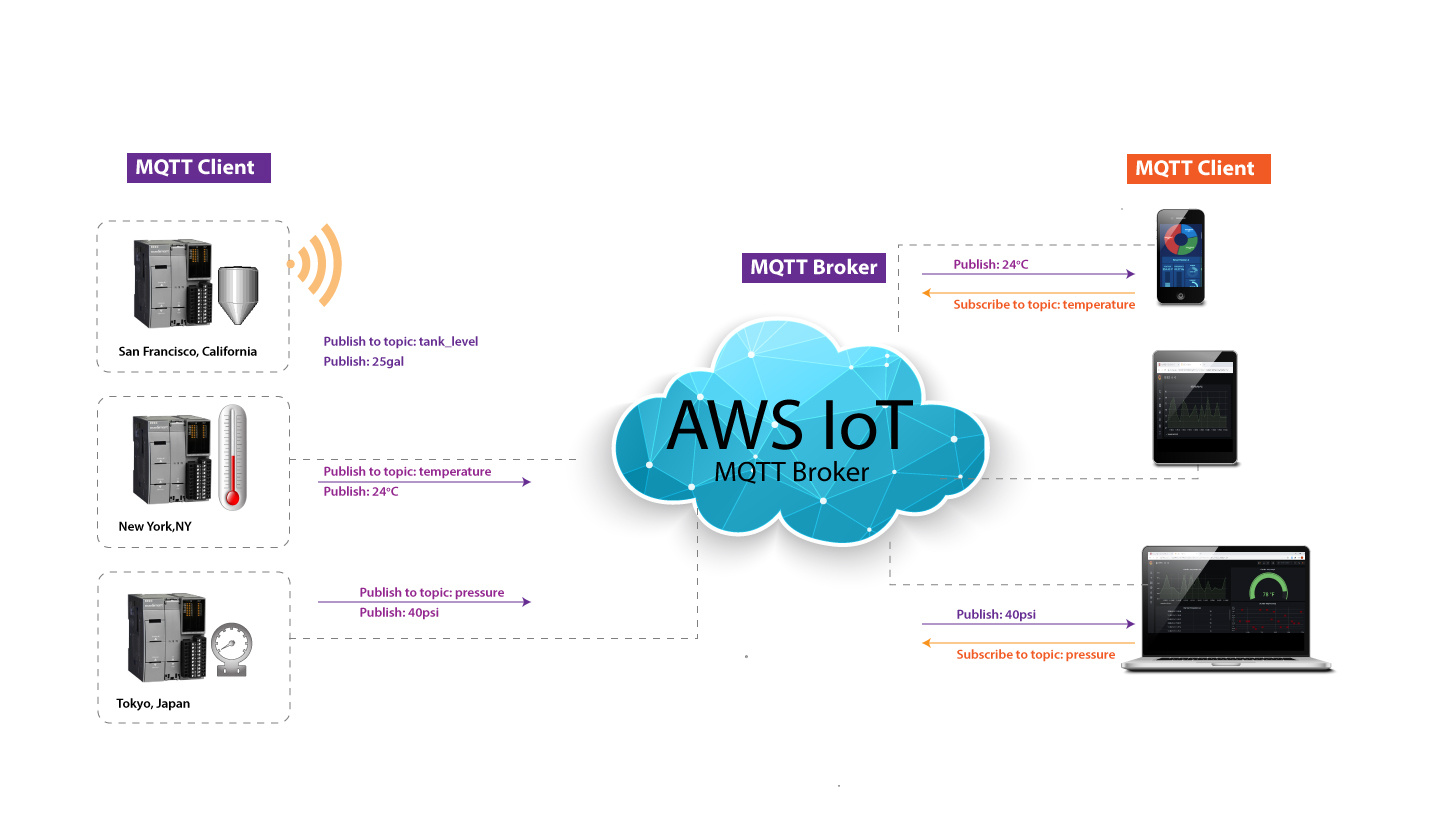
What is MQTT?
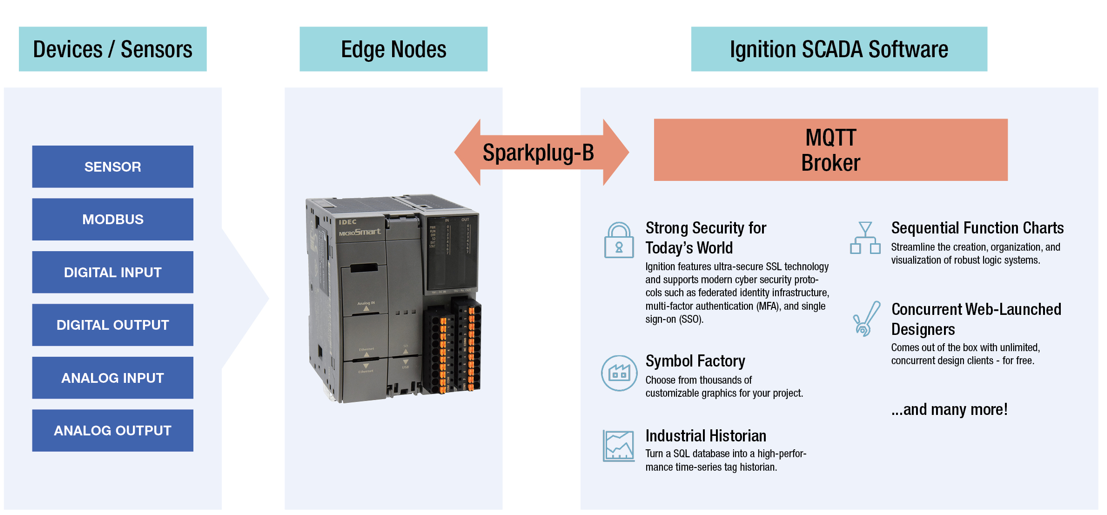
Sparkplug B
The FC6A Plus PLC now supports the Sparkplug B protocol, further elevating its IIoT capabilities.
Sparkplug B enables efficient and standardized communication for IIoT applications through the MQTT protocol. It facilitates seamless data exchange between the PLC and MQTT-enabled platforms like Ignition by utilizing a lightweight, state-aware messaging format. This functionality simplifies integration, enhances interoperability, and provides real-time insights for industrial automation systems.
With this new functionality, the FC6A Plus becomes an even more powerful solution for industries requiring efficient and reliable MQTT-based communication, such as oil and gas, water and wastewater treatment, automotive, and more.
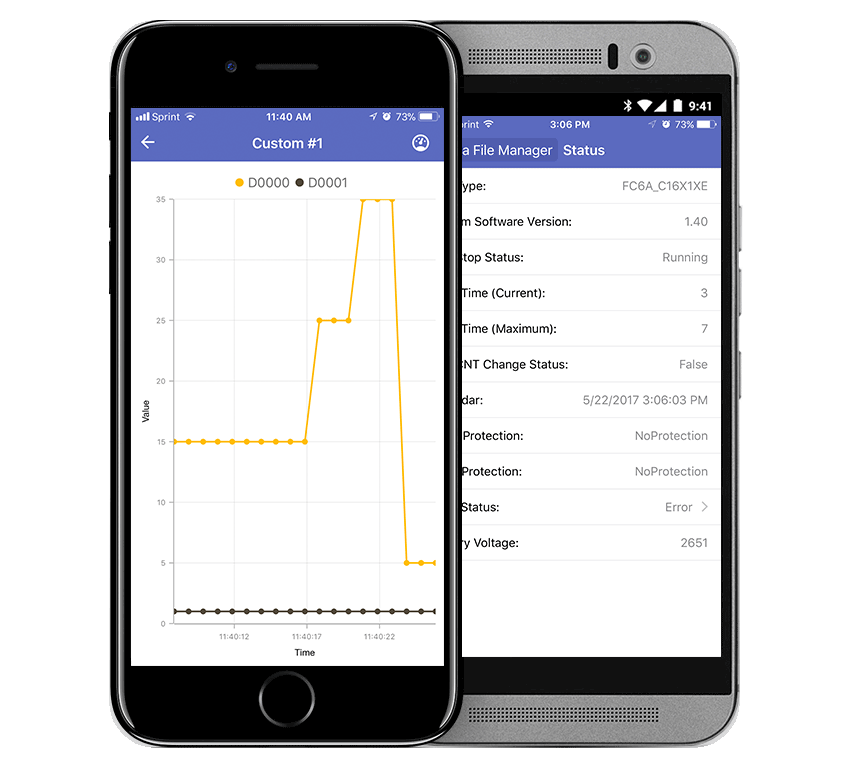
iOS and Android App
These free apps provide quick and convenient remote monitoring and control from smartphones and tablets. Users can upload and download PLC programs; monitor and update PLC status, data registers, internal relays, timers and counters, etc.; save, retrieve, and send files in cloud database such as Apple iCloud, Google Drive, Dropbox, etc.; access logged data and manage files in SD memory card; and download system firmware.
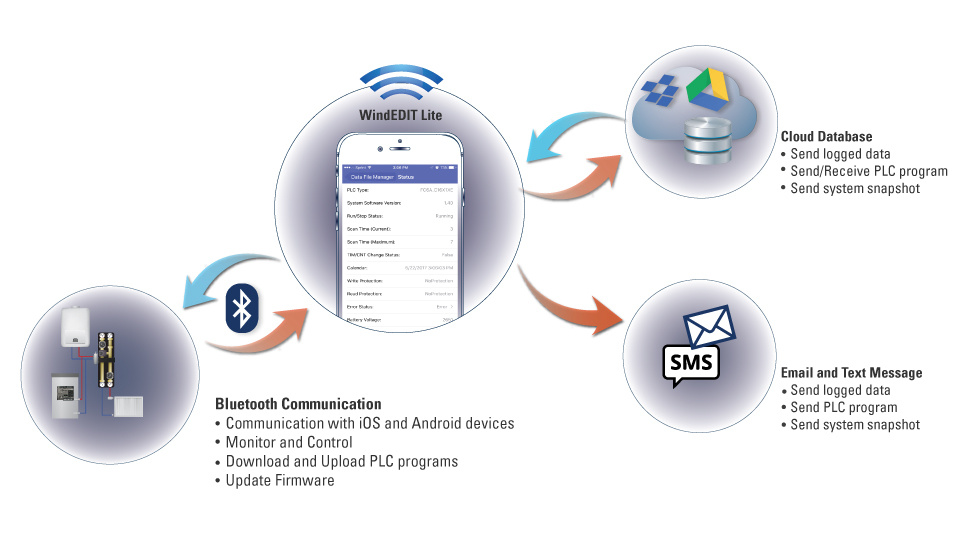
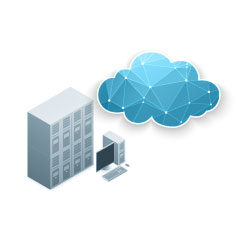
FTP Communication
MicroSmart FC6A Plus CPU can be configured as FTP Client or Server to allow transferring of ladder program and logged data between company server and MicroSmart FC6A. It’s an convenient and effective way to remotely stay on top of your control system.
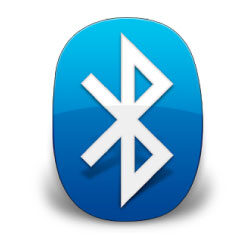
Bluetooth Communication
Bluetooth wireless communication with the MicroSmart FC6A Plus CPU can be established using the optional Bluetooth cartridge. Use your laptop/PC to monitor, download, and upload program wirelessly. Use your iOS and/or Android devices with Program File Manager tool to manage data in the PLC. Device such as bar code reader that’s equipped with Bluetooth capability can also be configured to communicate with the MicroSmart FC6A Plus CPU.
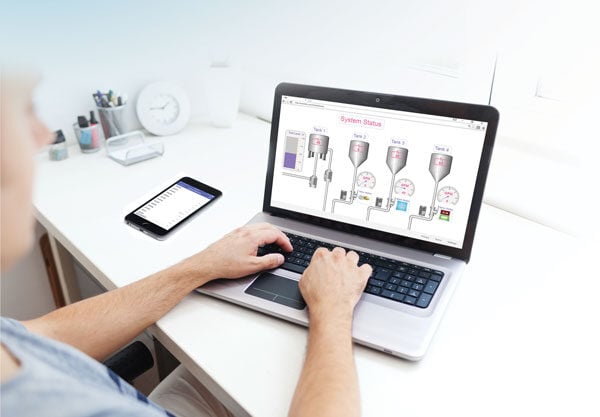
Web Server Functions
- The user can easily be connected to the FC6A using standard web browser on a PC or any mobile devices. A standard web page or custom web page can be accessed to monitor and update any PLC parameters.
- A built-in web page template is available if the user does not need to build his own.
- Custom web pages also can be constructed using the built-in web page editor in WindLDR software.
- The FC6A Plus has a built-in 5MB of memory to store the user’s web page.
- Additional memory can be utilized using optional SD memory card that supports up to 32GB.
Networking
EtherNet/IP
MicroSmart FC6A Plus CPUs now support EtherNet/IP™ protocol. With the addition of industry-standard EtherNet/IP™ scanner capabilities, the FC6A Plus can now connect with, monitor, and control any I/O, variable speed drive, or other intelligent automation device using this popular industrial protocol. In addition, the FC6A Plus can be configured as an EtherNet/IP™ adapter, allowing it to interact with other peer and supervisory systems, such as PLCs and HMIs.
Modbus TCP and RTU Protocol
FC6A supports both Modbus TCP and RTU. It can be easily be configured to be a Client (master) or Server (slave) on the Modbus network.
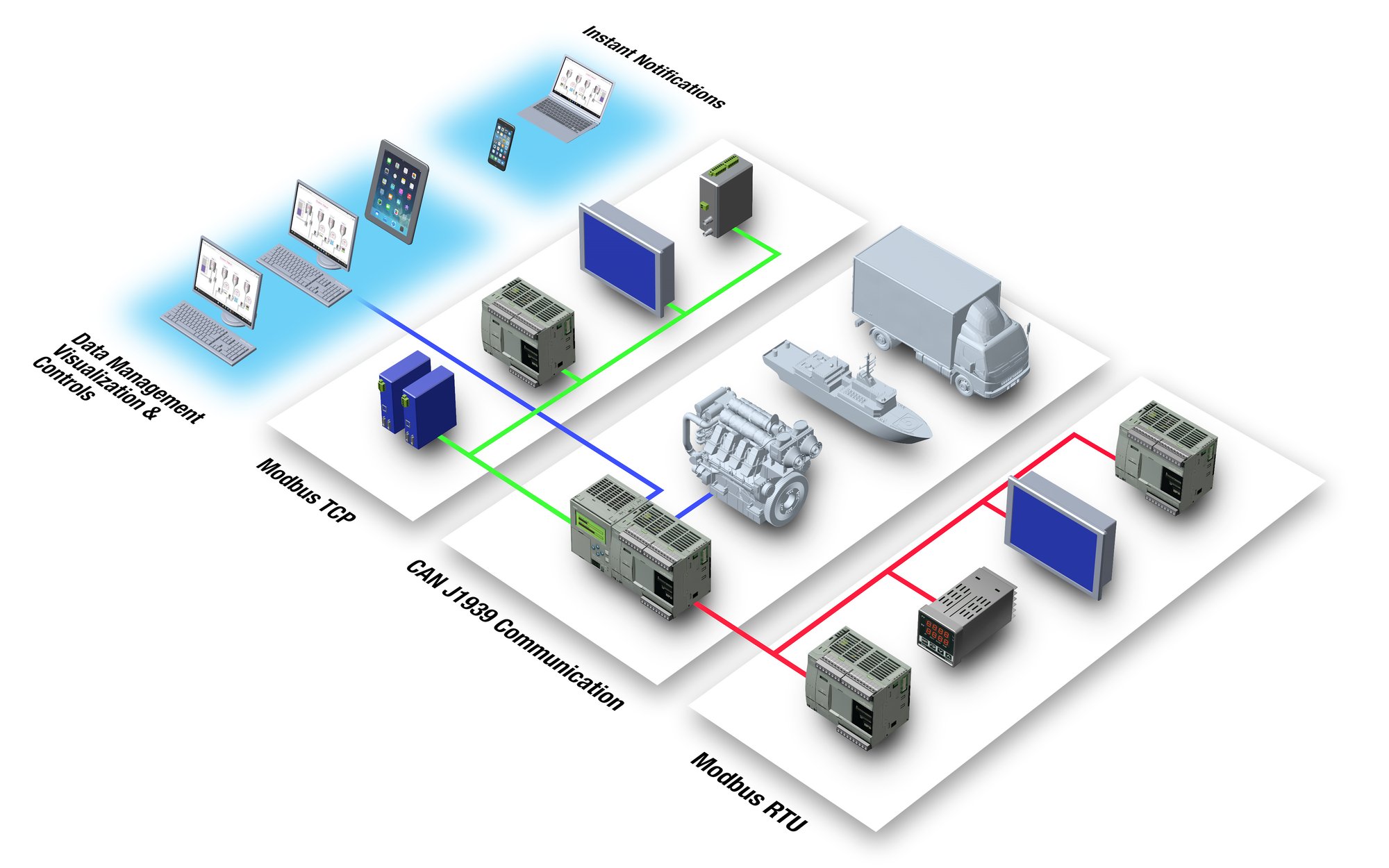
Programming
Web Page Editor
WindLDR version 8+ introduced a new Web Page Editor where anyone can use it to create professional and dynamic web pages to monitor and control the MicroSmart FC6A PLC.
Web Page Editor Tutorials
Ever wonder how you can create web page for your PLC without hiring an HTML and Java script expert?
Watch the videos below to see what you can do with web page editor!
Remote I/O System
Streamline your industrial processes with our cutting-edge Remote I/O System.
Our powerful SX8R bus coupler module offers significant efficiency enhancements for your systems. Paired with our MicroSmart FC6A I/O modules, it facilitates the seamless integration of a remote I/O system that can redefine your expectations.
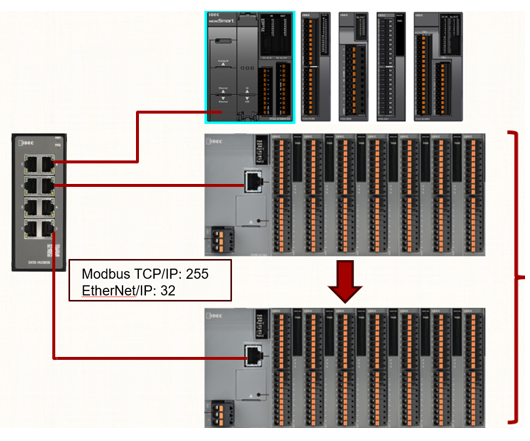
-1.jpg)
SX8R Bus Coupler Module
Our SX8R Bus Coupler offers the perfect blend of versatility, reliability, and performance, making it the ideal choice for industrial automation applications of any scale. Whether you're upgrading existing systems or building new installations, our Bus Coupler provides the connectivity and flexibility you need to succeed.
An exceptionally wide operating temperature range of -20 to +60 ˚C as well as IP20, and Class I Div 2 approval ratings, assures reliable operation in the toughest environment. This SX8R Bus Coupler is built for endurance and are backed by an industry-leading three-year warranty.
Experience seamless integration and enhanced efficiency with our Bus Coupler.
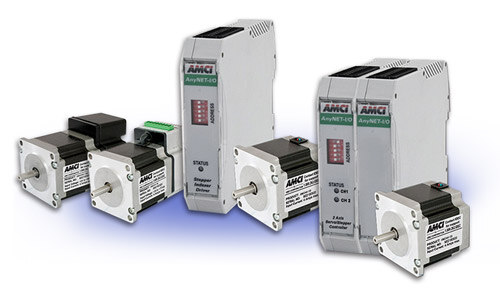
Many industrial applications require motion control, but users are often frustrated by the complexity and high cost of implementation. IDEC Corporation and AMCI, an established supplier of motion control systems, have partnered to address this issue by offering a simple yet highly capable stepper motion control system. This AMCI by IDEC product line includes controllers, stepper motors, a combo controller+drive, a combo drive+stepper motor, and the 3-in-1 controller+drive+stepper motor. When combined with an IDEC FC6A PLC and its embedded motion control software modules, these products allow users to quickly and simply implement single- and multi-axis motion control in a wide range of industries and applications.
What Makes Up a Stepper Motion System?
PLC
FC6A MicroSmart
MicroSmart FC6A , a powerful PLC with up to 520 digital I/O and 126 analog I/O. The MicroSmart FC6A provides the power of a PAC (programmable automation controller) in a low-cost controller with a small form factor, making it an ideal fit for demanding applications.
Controller - Network Type
FC6A MicroSmart
A 2-axis motion controller that can be expanded up to 12 axes. It can accept encoder feedback to provides stall detection and move verification. It includes six discrete inputs for move conditioning and other functions, and four discrete outputs to indicate status and provide diagnostics.
Drive+Controller
AMCI by IDEC’s integrated Stepper controller+drive combo is a ground-breaking approach to PLC-based motion control systems. With its servo performance in a stepper motion hardware, the IANG1 series can be expanded up to 6 axes
Stepper Motor+Drive+Controller
AMCI by IDEC’s controller+drive+motor combo unit provides all-in-one motion control with all the features of the two-axis controller, drive and stepper motor.
Drive
Stepper+Drive
AMCI by IDEC’s motor+drive combo unit can control one to six axes of motion, and it combines all the features of the two-axis controller and the drive into a single unit.
Drive+Controller
AMCI by IDEC’s integrated Stepper controller+drive combo is a ground-breaking approach to PLC-based motion control systems. With its servo performance in a stepper motion hardware, the IANG1 series can be expanded up to 6 axes
Stepper Motor+Drive+Controller
AMCI by IDEC’s controller+drive+motor combo unit provides all-in-one motion control with all the features of the two-axis controller, drive and stepper motor.
Motor
Stepper Motor
AMCI by IDEC’s stepper motor comes in standard NEMA 23 frame sizes with output torque rating of 130 and 240 oz-in.
Access Resources and Documents Available
FC6A Series MicroSmart Plus Catalog
Learn more about how the FC6A Series MicroSmart Plus is designed to meet the unique requirements of your business.
Smart Relays and Micro PLCs for Machine Control
Depending on your application requirements, there are different approaches to providing machine control. This article will help you better understand the pros and cons of two of the possibilities you may have to choose between.
When looking for the right controller option for your machine or system, you want a device that most closely matches the automation application it is going into. Since there is a wide variety of ways to go, we’ve chosen to focus on two of the more closely aligned options so that you can save money, complexity, and design time.
Edge Control
Edge control can take many forms to access stranded data, with modern PLCs often the preferred alternative.
For as long as operators have interacted with machinery and equipment, the concepts of the industrial ‘edge’ and ‘edge control’ have existed. Control at the edge could be an operator’s manual interaction with the equipment, or it could be hardwired controls performing some required functionality. A more sophisticated arrangement could consist of digital automation, typically with a programmable logic controller (PLC) monitoring input sensor at the edge, processing logic, and commanding outputs to control edge devices.
Lean Industrial IoT
End users can start introducing industrial IoT features with small steps to realize big value.
Internet of things (IoT) devices and apps are providing consumers with improved access to and control of their digital life. Common examples include residential smart systems like thermostats, appliances, and garage door openers—each of which can be viewed and operated via a mobile device.
Boiler Control System Uses Advanced PID Algorithm
System integrator Diverse Devices uses an IDEC automation system to control complex boiler installations used in hotels, hospitals, and other large facilities.
Founded in Los Angeles in 1946, Parker Boiler manufactures hot water and steam boilers used in manufacturing, wastewater treatment, heating large buildings ranging from hospitals to hotels, and other facilities worldwide.
IoT-Enabled PLC's for Smart Manufacturing
Every business wants to work ‘smarter’ to stay competitive in their field. That could mean streamlining their processes, using project management systems, or making the most of automation tools. In industrial settings, a smart manufacturing system can reduce labor costs, improve product quality control, lower the risk of accidents, and prevent wasted energy and resources.
Read the full article to learn more about how you can innovate your manufacturing for the demands of today.
IoT-Enabled PLC's for Predictive Maintenance
Factories and other work sites that use industrial machinery rely on equipment maintenance to keep things running smoothly. Each part and component will need servicing at some point – without any maintenance at all, every machine will eventually break down.
Read the full article to learn how to stay ahead of machine break downs with IoT-Enabled PLC's.
Compare IDEC FC6A MicroSmart vs.
Allen Bradley Micro830
Features | IDEC FC6A MicroSmart | Allen Bradley Micro830 |
CPU Module | 16 I/O (24 VDC, 100-240 VAC) 24 I/O (24 VDC, 100-240 VAC) 40 I/O(12 VDC, 24 VDC, 100-240 VAC) | 10 I/O (24 VAC/DC) 16 I/O (24 VAC/DC, 120 VAC) 24 I/O (240 VAC/DC) 48 I/O Brick (24 VAC/DC, 120 VAC) |
Processing Speed (basic instruction) | 0.042 µs | — |
Programming Memory | 640 kB (80,000 steps) | 2 kB |
Maximum Digital I/O | 528 | 48 |
Maximum Analog I/O | 127 | 20 |
Ethernet Port | Embedded, Optional 2nd Port | |
USB Port | ||
SD Memory Slot | ||
Programming Languages | Ladder Script | IEC61131-3: Ladder Diagram, Function Block Diagram, Structured Text |
Communication Protocol | Modbus TCP Modbus RTU/ASCII CAN J1939 | Modbus TCP Modbus RTU/ASCII DeviceNet Master/Slave (plug-in module) |
High Speed Counter | 6 x 100 kHz | 6 x 100 kHz |
High Speed Output | 4 x 100 kHz | 3 x 100 kHz |
Web Server Function | ||
User Web Page |
Allen Bradley Micro850
Features | IDEC FC6A MicroSmart | Allen Bradley Micro850 |
CPU Module | 16 I/O (24 VDC, 100-240 VAC) 24 I/O (24 VDC, 100-240 VAC) 40 I/O(12 VDC, 24 VDC, 100-240 VAC) | 24 I/O (24 VAC/DC) 48 I/O (24 VAC/DC, 120 VAC) |
Processing Speed (basic instruction) | 0.042 µs | — |
Programming Memory | 640 kB (80,000 steps) | 2 kB |
Maximum Digital I/O | 528 | 132 |
Maximum Analog I/O | 127 | 52 |
Ethernet Port | Embedded, Optional 2nd Port | Embedded |
USB Port | ||
SD Memory Slot | ||
Programming Languages | Ladder Script | IEC61131-3: Ladder Diagram, Function Block Diagram, Structured Text |
Communication Protocol | Modbus TCP Modbus RTU/ASCII CAN J1939 | Modbus TCP Modbus RTU/ASCII DeviceNet Master/Slave (plug-in module) EtherNet/IP |
High Speed Counter | 6 x 100 kHz | 6 x 100 kHz |
High Speed Output | 4 x 100 kHz | 3 x 100 kHz |
Web Server Function | ||
User Web Page |
Allen Bradley MicroLogiz 1100
Features | IDEC FC6A MicroSmart | Allen Bradley MicroLogix 1100 |
CPU Module | 16 I/O (24 VDC, 100-240 VAC) 24 I/O (24 VDC, 100-240 VAC) 40 I/O(12 VDC, 24 VDC, 100-240 VAC) | 18 I/O (24 VDC, 100-240 VAC) |
Processing Speed (basic instruction) | 0.042 µs | 1.5 µs |
Programming Memory | 640 kB (80,000 steps) | 4 kB |
Maximum Digital I/O | 528 | 144 |
Maximum Analog I/O | 127 | 18 |
Ethernet Port | Embedded, Optional 2nd Port | Embedded |
USB Port | ||
SD Memory Slot | ||
Programming Languages | Ladder Script | Ladder |
Communication Protocol | Modbus TCP Modbus RTU/ASCII CAN J1939 | Modbus RTU/ASCII DeviceNet EtherNet/IP |
High Speed Counter | 6 x 100 kHz | 4 x 20 kHz |
High Speed Output | 4 x 100 kHz | 2 x 20 kHz |
Web Server Function | ||
User Web Page |
Allen Bradley MicroLogix 1200
Features | IDEC FC6A MicroSmart | Allen Bradley MicroLogix 1200 |
CPU Module | 16 I/O (24 VDC, 100-240 VAC) 24 I/O (24 VDC, 100-240 VAC) 40 I/O(12 VDC, 24 VDC, 100-240 VAC) | 24 I/O (24 VDC, 100-240 VAC) 40I/O (24 VDC, 100-240 VAC) |
Processing Speed (basic instruction) | 0.042 µs | 0.9 µs |
Programming Memory | 640 kB (80,000 steps) | 4 kB |
Maximum Digital I/O | 528 | 136 |
Maximum Analog I/O | 127 | 24 |
Ethernet Port | Embedded, Optional 2nd Port | Serial-to-Ethernet module |
USB Port | ||
SD Memory Slot | ||
Programming Languages | Ladder Script | Ladder |
Communication Protocol | Modbus TCP Modbus RTU/ASCII CAN J1939 | Modbus RTU/ASCII DeviceNet EtherNet/IP |
High Speed Counter | 6 x 100 kHz | 4 x 20 kHz |
High Speed Output | 4 x 100 kHz | 1 x 20 kHz |
Web Server Function | ||
User Web Page |
Allen Bradley MicroLogix 1400
Features | IDEC FC6A MicroSmart | Allen Bradley MicroLogix 1400 |
CPU Module | 16 I/O (24 VDC, 100-240 VAC) 24 I/O (24 VDC, 100-240 VAC) 40 I/O(12 VDC, 24 VDC, 100-240 VAC) | 32 I/O (24 VDC, 100-240 VAC) 38 I/O (24 VDC, 100-240 VAC) |
Processing Speed (basic instruction) | 0.042 µs | 0.26 µs |
Programming Memory | 640 kB (80,000 steps) | 10 kB |
Maximum Digital I/O | 528 | 256 |
Maximum Analog I/O | 127 | 32 |
Ethernet Port | Embedded, Optional 2nd Port | Embedded |
USB Port | ||
SD Memory Slot | ||
Programming Languages | Ladder Script | Ladder |
Communication Protocol | Modbus TCP Modbus RTU/ASCII CAN J1939 | Modbus RTU/ASCII DeviceNet EtherNet/IP DNP3 Slave |
High Speed Counter | 6 x 100 kHz | 6 x 100 kHz |
High Speed Output | 4 x 100 kHz | 3 x 100 kHz |
Web Server Function | ||
User Web Page |
Siemens S7-1200
Features | IDEC FC6A MicroSmart | Siemens S7-1200 |
CPU Module | 16 I/O (24 VDC, 100-240 VAC) 24 I/O (24 VDC, 100-240 VAC) 40 I/O(12 VDC, 24 VDC, 100-240 VAC) | 10 I/O (24 VDC, 100-240 VAC) 14 I/O (24 VDC, 100-240 VAC) 24 I/O (24 VDC, 100-240 VAC) |
Processing Speed (basic instruction) | 0.042 µs | — |
Programming Memory | 640 kB (80,000 steps) | 50 kB |
Maximum Digital I/O | 528 | 284 |
Maximum Analog I/O | 127 | 51 |
Ethernet Port | Embedded, Optional 2nd Port | Embedded |
USB Port | ||
SD Memory Slot | ||
Programming Languages | Ladder Script | Ladder |
Communication Protocol | Modbus TCP Modbus RTU/ASCII CAN J1939 | Modbus TCP Modbus RTU Profibus |
High Speed Counter | 6 x 100 kHz | 3 x 100 kHz, 3 x 30 kHz |
High Speed Output | 4 x 100 kHz | 2 x 100 kHz |
Web Server Function | ||
User Web Page |
Automation Direct DL05
Features | IDEC FC6A MicroSmart | Automation Direct DL05 |
CPU Module | 16 I/O (24 VDC, 100-240 VAC) 24 I/O (24 VDC, 100-240 VAC) 40 I/O(12 VDC, 24 VDC, 100-240 VAC) | 14 I/O (12-24 VDC, 100-240 VAC) |
Processing Speed (basic instruction) | 0.042 µs | 100 µs |
Programming Memory | 640 kB (80,000 steps) | 12 kB (2,048 steps) |
Maximum Digital I/O | 528 | 30 |
Maximum Analog I/O | 127 | 8 |
Ethernet Port | Embedded, Optional 2nd Port | Optional Expansion module |
USB Port | ||
SD Memory Slot | ||
Programming Languages | Ladder Script | Ladder |
Communication Protocol | Modbus TCP Modbus RTU/ASCII CAN J1939 | Modbus TCP Modbus RTU/ASCII DeviceNet (slave) Profibus (slave) |
High Speed Counter | 6 x 100 kHz | 1 x 5 kHz |
High Speed Output | 4 x 100 kHz | 1 x 7 KHz |
Web Server Function | ||
User Web Page |
Automation Direct DL06
Features | IDEC FC6A MicroSmart | Automation Direct DL06 |
CPU Module | 16 I/O (24 VDC, 100-240 VAC) 24 I/O (24 VDC, 100-240 VAC) 40 I/O(12 VDC, 24 VDC, 100-240 VAC) | 36 I/O (12-24 VDC, 100-240 VAC) |
Processing Speed (basic instruction) | 0.042 µs | 70 µs |
Programming Memory | 640 kB (80,000 steps) | 30 kB (7,680 steps) |
Maximum Digital I/O | 528 | 100 |
Maximum Analog I/O | 127 | 32 |
Ethernet Port | Embedded, Optional 2nd Port | Optional Expansion module |
USB Port | ||
SD Memory Slot | ||
Programming Languages | Ladder Script | Ladder |
Communication Protocol | Modbus TCP Modbus RTU/ASCII CAN J1939 | Modbus TCP Modbus RTU/ASCII DeviceNet (slave) Profibus (slave) |
High Speed Counter | 6 x 100 kHz | 1 x 5 kHz |
High Speed Output | 4 x 100 kHz | 1 x 7 KHz |
Web Server Function | ||
User Web Page |
Automation Direct DL205
Features | IDEC FC6A MicroSmart | Automation Direct DL205 |
CPU Module | 16 I/O (24 VDC, 100-240 VAC) 24 I/O (24 VDC, 100-240 VAC) 40 I/O(12 VDC, 24 VDC, 100-240 VAC) | CPU Only |
Processing Speed (basic instruction) | 0.042 µs | 0.61 µs |
Programming Memory | 640 kB (80,000 steps) | 31.6 kB |
Maximum Digital I/O | 528 | 256 |
Maximum Analog I/O | 127 | — |
Ethernet Port | Embedded, Optional 2nd Port | Optional Expansion module |
USB Port | ||
SD Memory Slot | ||
Programming Languages | Ladder Script | Ladder |
Communication Protocol | Modbus TCP Modbus RTU/ASCII CAN J1939 | Modbus TCP Modbus RTU/ASCII DeviceNet (slave) Profibus (slave) |
High Speed Counter | 6 x 100 kHz | Optional HSC Module |
High Speed Output | 4 x 100 kHz | — |
Web Server Function | ||
User Web Page |
Automation Direct CLICK
Features | IDEC FC6A MicroSmart | Automation Direct CLICK |
CPU Module | 16 I/O (24 VDC, 100-240 VAC) 24 I/O (24 VDC, 100-240 VAC) 40 I/O(12 VDC, 24 VDC, 100-240 VAC) | 14 I/O (24 VDC) 12 I/O w/Analog (24 VDC) |
Processing Speed (basic instruction) | 0.042 µs | 5 µs |
Programming Memory | 640 kB (80,000 steps) | 8,000 steps |
Maximum Digital I/O | 528 | 142 |
Maximum Analog I/O | 127 | 32 |
Ethernet Port | Embedded, Optional 2nd Port | |
USB Port | ||
SD Memory Slot | ||
Programming Languages | Ladder Script | Ladder |
Communication Protocol | Modbus TCP Modbus RTU/ASCII CAN J1939 | Modbus RTU/ASCII |
High Speed Counter | 6 x 100 kHz | |
High Speed Output | 4 x 100 kHz | |
Web Server Function | ||
User Web Page |